Filtration in hydraulic systems is an essential component to ensure the system’s efficiency, durability, and reliability. Hydraulic systems, which operate under high pressure and with moving fluids, are prone to the accumulation of contaminants such as metal particles, dust, water, and other pollutants. These elements can cause premature wear of components, reduce energy efficiency, and compromise system safety.
The FMS International approach to filtration management in hydraulic systems is based on four fundamental pillars: parameter definition, clean start, effective monitoring, and staying clean. These principles ensure that the hydraulic system operates optimally throughout its service life.
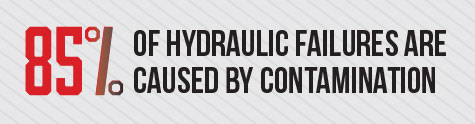
1. Parameters
Most hydraulic systems (85%) fail due to contamination issues, and lubricants often require premature replacement for the same reason. For this reason, ISO 4406 parameters have been defined for hydraulic system components.
2. Clean Start
New lubricants often fail to meet ISO cleanliness standards and should enter the equipment with a code no higher than 16/14/12. However, achieving this goal requires dealing with low temperatures (viscosity) when filtering new oil.
3. Effective monitoring
Monitoring practices are often NOT the most effective, as sampling methodologies can alter results, and even more critically, there may be no predictive solutions in place to help mitigate results that fall outside the optimal ISO parameters specified by OEMs.
1
Definition of
parameters
The first phase of the filtration process is the definition of parameters. Before installing any filtration system, it is crucial to define which contaminants could affect the system’s performance and what levels of cleanliness are required. Key parameters include:
- PARTICLE SIZE: determine the range of particle sizes that can enter the system and must be removed. hydraulic systems typically need to filter particles ranging from micrometers to millimeters, depending on the sensitivity of the components.
- HYDRAULIC FLUID CONTAMINATION LEVEL ACCORDING TO ISO 4406: The ISO 4406 standard provides a classification system for the contamination level of hydraulic fluids, based on the number of particles present in the fluid. The standard divides particles into three sizes:

VISUAL COMPARISON OF CLEANLINESS IN ISO 4406 CODES












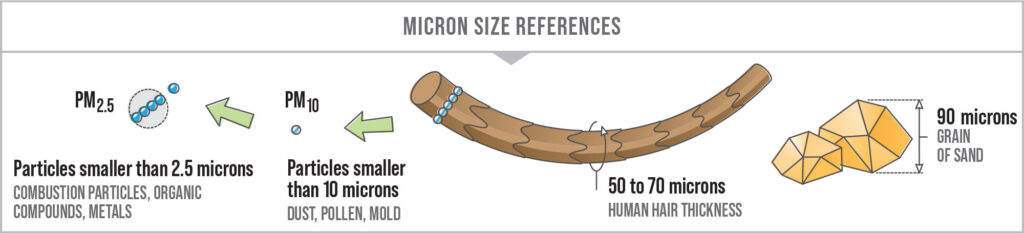
According to this standard, hydraulic fluids are classified into different contamination levels depending on the number of particles present in each of these categories. This classification allows specifying the required cleanliness level for each hydraulic system, optimizing the selection of the filter type and the maintenance frequency.
- VISCOSITY OF THE FLUID: Hydraulic systems operate with a variety of fluids that vary in viscosity. The viscosity of the fluid affects the filter’s ability to efficiently remove particles.
- SYSTEM FLOW: The fluid flow rate in the system must be considered when selecting the type and size of the filter. Very high flow may require larger filters or multiple filters in parallel to avoid clogging.
2
CLEAN
START
The Clean Start principle refers to the implementation of measures to ensure that the system is free from contaminants from the start of its operation. This phase is essential to ensure that contaminants do not enter the system during installation or startup.
SOME KEY ASPECTS OF “CLEAN START” INCLUDE:
- PRE-CLEANING OF COMPONENTS: Ensuring that all hydraulic components (pipes, valves, pumps, etc.) are free of particles and dirt before system installation. It is recommended to use cleaning procedures such as washing with specialized cleaning fluids or compressed air.
- USE OF FILTERS IN THE START-UP PHASE: Installing temporary filters to capture any particles that may detach during installation. These filters should have a low clogging capacity to avoid interfering with the system’s startup.
- HYDRAULIC FLUID QUALITY: Ensuring that the hydraulic fluid used from the beginning is of high quality and suitable for the system’s specifications, free from previous contaminants.
3
Effective
monitoring
Effective monitoring is key to ensuring that the hydraulic system maintains an adequate level of cleanliness during its operation. Filtration is not a static process; it requires constant monitoring to ensure that the filters are functioning properly.
SOME EFFECTIVE MONITORING METHODS INCLUDE:
- DIFFERENTIAL PRESSURE MONITORING: Monitoring pressure through the differential between the filter’s inlet and outlet is a key indicator of its performance. An increase in differential pressure may indicate that the filter is clogged and needs to be replaced or cleaned.
- FLUID ANALYSIS: Performing periodic analysis of the hydraulic fluid to detect the presence of contaminants such as metal particles or water. This analysis can be conducted through laboratory tests or by using inline particle sensors.
- PERIODIC ISO4406 CODE MEASUREMENTS: Integrating laser particle counters into the system to provide real-time data on the concentration of particles in the fluid. These counters help identify issues before they cause significant damage and, most importantly, evaluate whether the bypass filter is performing its intended function.
- REMOTE MONITORING: Implementing remote monitoring systems that allow operators to check the system’s status from distant locations. This is useful for equipment in hard-to-reach areas or when constant supervision is required.
4
Staying
clean
The final principle of the FMS International methodology is Staying Clean, which refers to the regular maintenance of the filtration system to ensure its efficient operation over time. This involves the installation of high-efficiency filters, which must be capable of controlling particles more effectively in the system, always preceded by proper dialysis with ISO 4406 certification.
THE OPTIONS AVAILABLE TO ENSURE HIGH-EFFICIENCY FILTRATION INCLUDE:
- HIGH-EFFICIENCY BYPASS FILTER (does not require modifying the original machine setup).
- HIGH-EFFICIENCY SUCTION AND PRESSURE FILTER (requires changing the current machine setup).
- HIGH-EFFICIENCY RETURN FILTER (when possible, without the need to modify the original machine setup).
NOTE: There are stationary units that can use a recirculator to improve the filtration system’s performance.
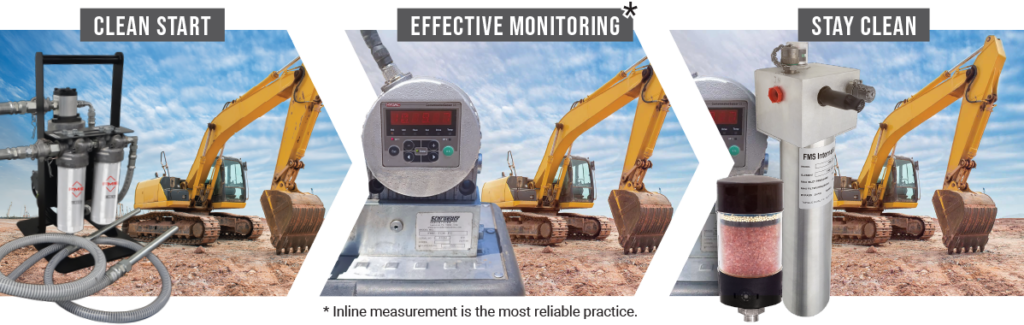
SOME KEY POINTS FOR “STAYING CLEAN” INCLUDE:
- REGULAR PREVENTIVE MAINTENANCE: Establish a preventive maintenance program that includes periodic cleaning or replacement of filters, checking the fluid condition, and verifying the monitoring system.
- FILTER REPLACEMENT: Filters should be replaced according to the manufacturer’s recommendations or when monitoring indicates that the filter’s capacity has been exceeded.
- CONTROL OF EXTERNAL CONTAMINATION: Reduce the entry of external contaminants into the system through measures such as properly sealing system inlets, controlling air quality with specialized breathers that prevent the ingress of particles and moisture.
- STAFF TRAINING: Ensure that all personnel involved in the maintenance of hydraulic systems are trained in best practices to keep systems clean, from handling filters to properly installing components.
CONCLUSION
Filtration in hydraulic systems is essential to ensure the longevity, efficiency, and safety of equipment. By applying the FMS International methodology, which focuses on Parameter Definition, Clean Start, Effective Monitoring, and Staying Clean, the performance of hydraulic systems can be significantly improved, and operational costs resulting from failures and expensive repairs can be reduced. The implementation of these practices not only prevents damage from contaminants but also optimizes system performance throughout its service life.