Negative Impacts of Diesel Contaminated
by Particles According to ISO 4406*
Diesel contaminated by particles represents a significant issue for any operation involving internal combustion engines. ISO 4406 sets standards for classifying particle contamination in oil-based fluids, but its relevance extends to diesel fuel, as the presence of particles can have negative impacts on:
Operational efficiency (Higher Fuel Consumption)
Energy efficiency and engine power
Service life of the injection system, engine, and lubricant
Environmental pollution
Health impacts on the community
IMPACTS
ON OPERATIONAL EFFICIENCY
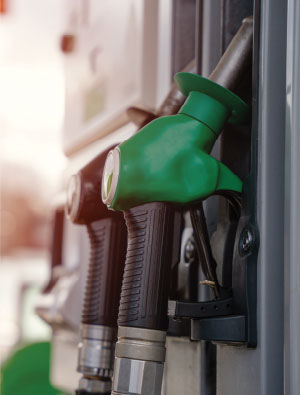
ON ENGINE
LIFESPAN
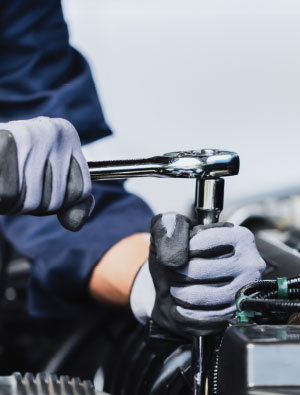
ON THE
ENVIRONMENT
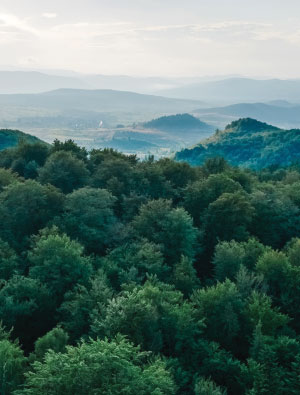
ON
HEALTH
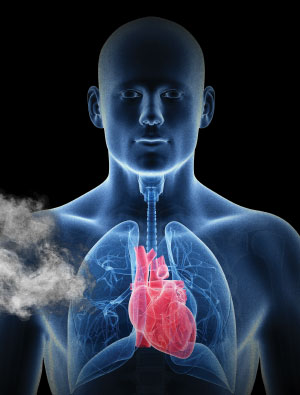
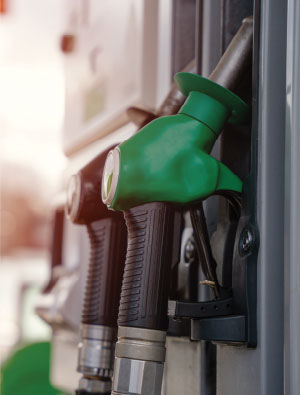
IMPACTS ON
OPERATING EFFICIENCY
INCREASED FUEL CONSUMPTION
Contaminated diesel due to particles can have a direct impact on the operational efficiency of diesel engines. Particles present in the fuel can clog filters, injectors, and other components of the fuel system, resulting in decreased engine performance and increased fuel consumption. This clogging can lead to incomplete combustion, causing soot buildup and reduced engine power. Therefore, particle-contaminated diesel, according to ISO 4406 standards, can lead to a significant decrease in the operational efficiency of diesel vehicles, which in turn results in higher operating and maintenance costs.
THE 4 STEPS OF POWER LOSS
POOR
DOSING
POOR DOSING
Injection systems require ISO 11/8/7 diesel to optimally dose the fuel. Poor injector dosing due to the presence of particles results in power loss and consequently up to 5% higher fuel consumption.
LOSS OF COMPRESSION
LOSS OF COMPRESSION
Particles in the combustion chamber cause premature wear on the cylinders, leading to early compression loss—synonymous with power loss and increased fuel consumption throughout the engine’s service life, by up to 7%.
CONTAMINATED LUBRICANT
CONTAMINATED LUBRICANT
Particle-contaminated lubricant increases friction and temperature, causing up to 2–3% power loss and higher fuel consumption.
PREMATURE DPF SATURATION
PREMATURE DPF SATURATION
Pressure drop in diesel particulate filters (DPFs) causes up to 2% power loss and increased fuel consumption due to combusted particles.
IMPACTS ON
ENGINE LIFESPAN
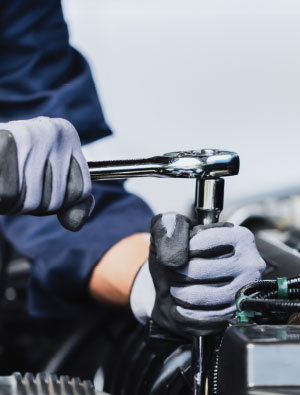
The presence of particles in diesel fuel can also have direct consequences on engine performance. abrasive particles can cause accelerated wear on components such as cylinders, pistons, and rings, resulting in reduced engine lifespan and increased repair and replacement costs. additionally, particles in diesel can interfere with engine lubrication, leading to greater wear and damage to internal components, and even degrading lubricant additives—reducing oil change intervals. in summary, particle-contaminated diesel, as classified under iso 4406, can significantly decrease the performance and lifespan of diesel engines, affecting the reliability and durability of vehicles and machinery.
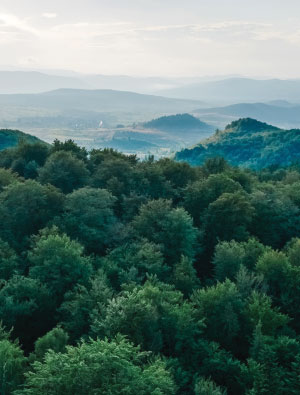
Impacts on the
Environment
In addition to impacts on operational efficiency and engine performance, particle-contaminated diesel also has significant environmental consequences. particles present in diesel can contribute to the release of pollutants into the atmosphere, affecting air quality and posing public health risks. incomplete combustion caused by the presence of particles can lead to increased emissions of exhaust gases, including nitrogen oxides (nox) and soot particles, both known for their harmful effects on human health and the environment. therefore, particle-contaminated diesel represents a serious environmental concern, and compliance with the iso 4406 standard is essential to minimize these impacts.
IMPACTS
ON HEALTH
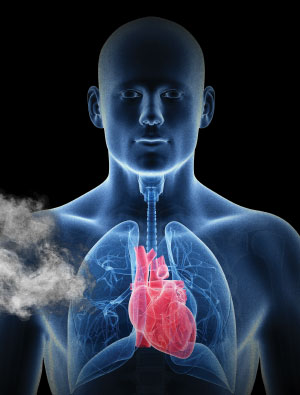
Diesel contaminated with particles poses a serious threat to human health, as the microscopic particles present in this fuel can penetrate deep into the lungs when inhaled. The World Health Organization (WHO) reports that premature deaths caused by particulate matter emitted by engines reach 4.2 million annually. Chronic exposure to the particles found in contaminated diesel can lead to various respiratory issues such as chronic bronchitis, asthma, and even an increased risk of developing lung cancer. Additionally, these particles can travel through the bloodstream and affect other organs, contributing to cardiovascular diseases and nervous system complications.
The most vulnerable groups to these impacts include children, the elderly, and individuals with preexisting respiratory conditions. Therefore, it is crucial to implement strict diesel quality control measures to ensure compliance with the standards set by ISO 4406, in order to protect public health from the harmful effects associated with particle contamination.
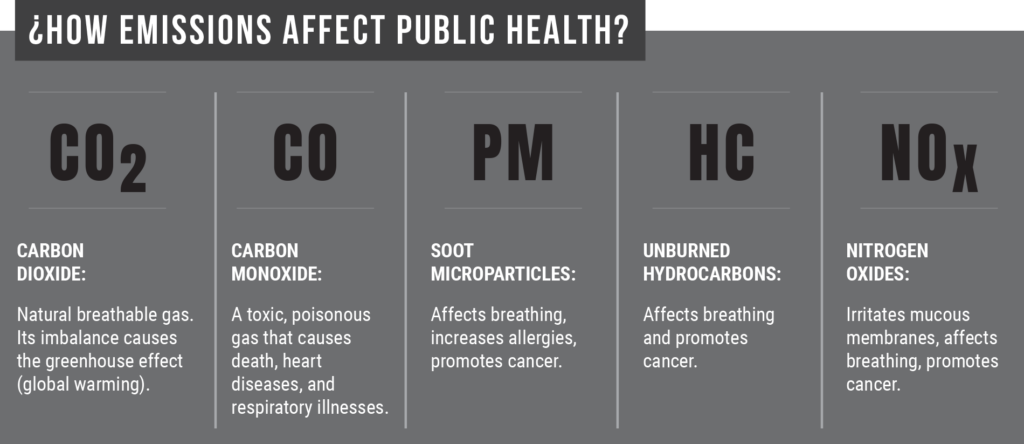
COMPLIANCE WITH ISO 4406 STANDARD
The ISO 4406 standard establishes a method for classifying particle contamination in fluids, including diesel fuel. It defines the size and quantity of particles allowed in the fuel, providing a clear guideline to ensure the quality and cleanliness of diesel used in diesel engines. Compliance with this standard is essential to prevent the negative impacts of particle-contaminated diesel, as it sets clear benchmarks for fuel quality and contributes to engine protection, operational efficiency, and environmental preservation.
Recommendations and Conclusions
To mitigate the negative impacts of particle-contaminated diesel according to ISO 4406, careful attention must be given to the quality of the diesel fuel used in engines, along with the proper selection of ultrafiltration systems that meet high-efficiency standards such as THETA 4 > 4000 (in a single pass) and BETA 4 > 4000 (in recirculation). Additionally, when selecting filtration systems, it is essential to include filters that comply with SAE J1488 standards to effectively mitigate the presence of water in oil-based fluids.
It is recommended to perform regular diesel quality testing in accordance with ISO 4406 to ensure compliance with cleanliness and purity standards. Moreover, maintaining a preventive maintenance program—including the inspection and replacement of filters and fuel system components—is critical to avoiding particle contamination. The use of advanced fuel filtration and purification technologies can also play a significant role in preventing particle contamination and protecting diesel engines.
In conclusion, diesel contaminated by particles as defined by ISO 4406 represents a serious threat to operational efficiency, engine performance, and the environment. Adhering to the standards established by ISO 4406 is essential for minimizing these impacts and ensuring optimal performance of diesel engines. By adopting effective maintenance and quality control practices, it is possible to mitigate the negative impacts of contaminated diesel and promote reliable, sustainable performance in diesel engines across various industrial sectors.
OEMs have established ISO 18/16/13 as the MAXIMUM LIMIT and ISO 11/8/7 as the OPTIMAL standard, while in Latin America, the average diesel fuel consumed has a cleanliness level of ISO 22/20/17—between 1,000 and 2,000 times more contaminated than the established optimal level.
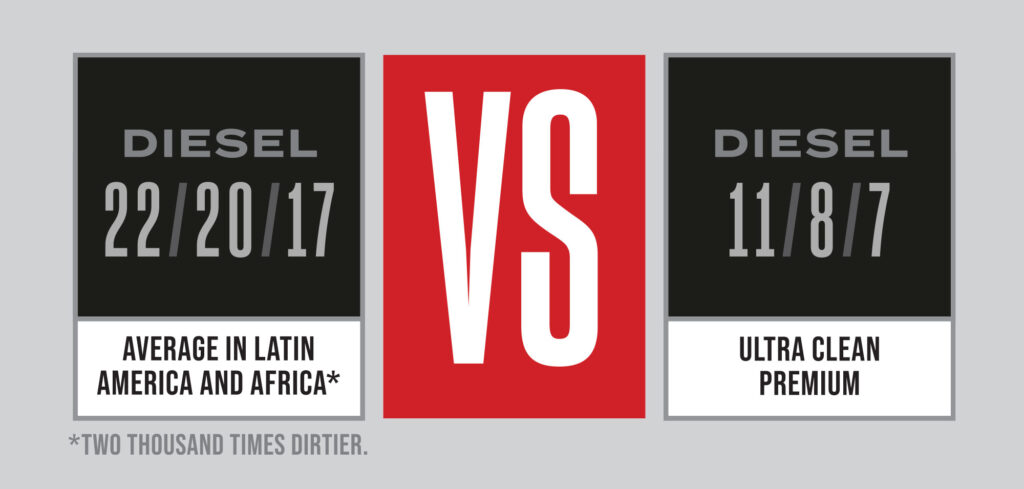